Control development
For us, the essential tasks of the control are an intelligent use of the high-pressure system and a stable communication with the machine tool
// in order to implement targets of the machinery directive as well as to identify system faults and thus ensure the safety of the machine and the production process.
// in order to make the production process as energy-efficient as possible thanks to the intelligently designed control possibilities (commands, parameterisation, etc.).
Electric filter contamination indicator

The contamination rate of the filter is measured by means of an integrated differential pressure switch, from a certain value on, an alarm is signaled to the machine.
Controllable service connections
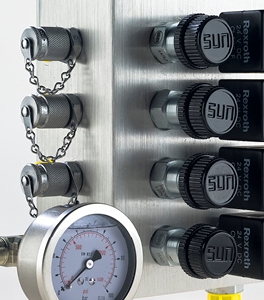
On the machine side, as many free control codes (e.g. M functions) are required as controllable high-pressure service connections are demanded.
Electronic control
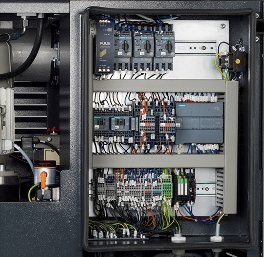
Constantly in connection with the machine control, this programmable logic control centre is the brain of the cooling lubricant high-pressure system. It monitors the level in the clean liquid tank, sequentially or jointly activates the high-pressure service connections as required, controls the feed pump, commands the automatic cleaning of the filter and communicates the operating state of the device.
Pressure control (mechanic / electronic)
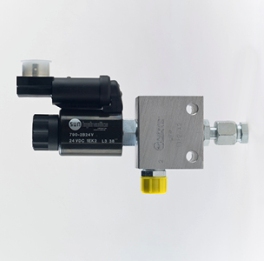
- Pressure controller at the high-pressure service connection – the easiest type of pressure control.
- If a certain tool or turret is to be provided with different pressures freely selectable via the machine program, the combination of several service connections to one or several high-pressure lines into the machine is the preferred variant. The selection is made via free control codes (e.g. M functions) in the machine.
- A third possibility: Smooth pressure setting directly via the machine program. For this purpose the control of the machine tool must be able to generate the respective commands.
Frequency-controlled drive
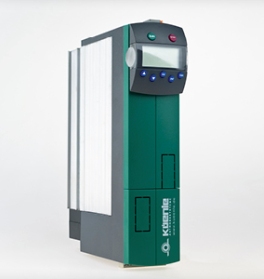
In this case the speed of the pump drive motor is changed. The nominal speed can be defined via command from the machine control or simply by a setting on the high-pressure unit. This method serves to adjust the discharge to the machining requirements. This control type comes to its limits in case of small speeds, as the performance of common asynchronous motors noticeably drops in this range.