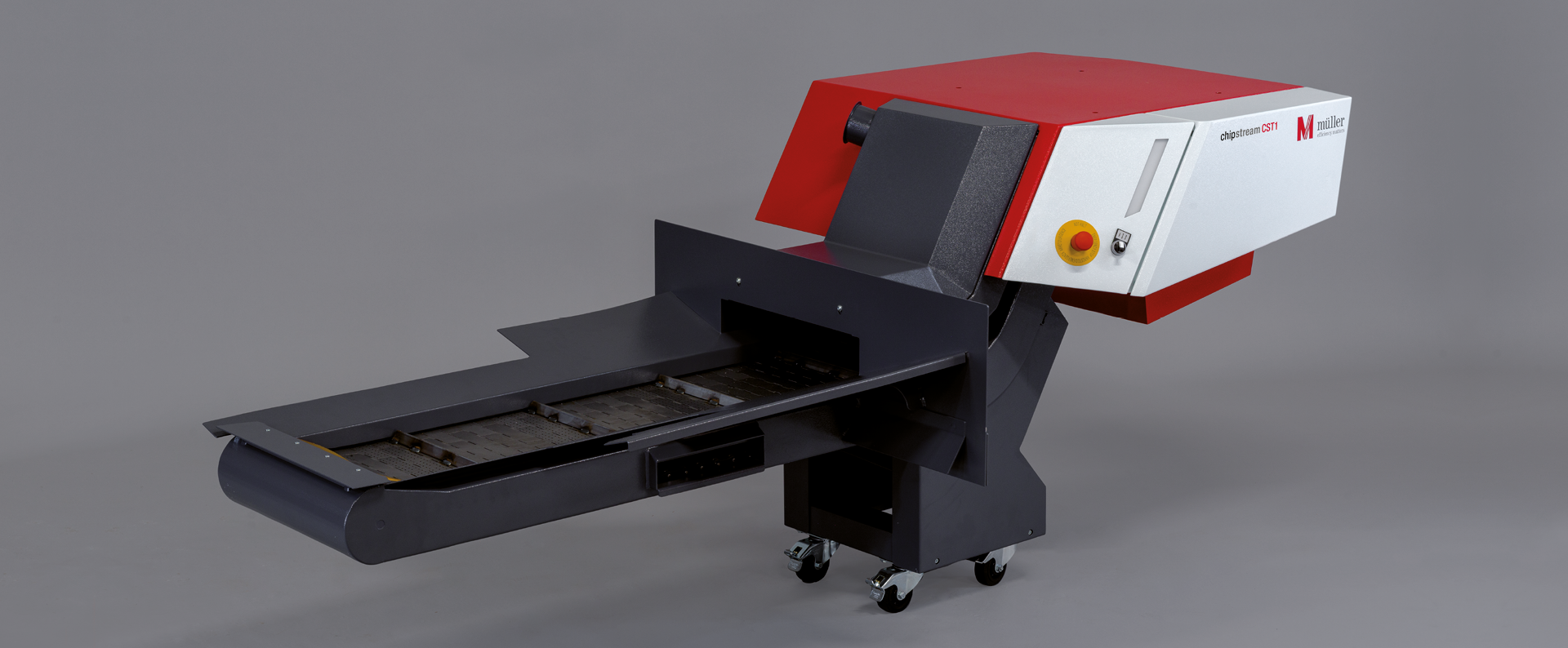
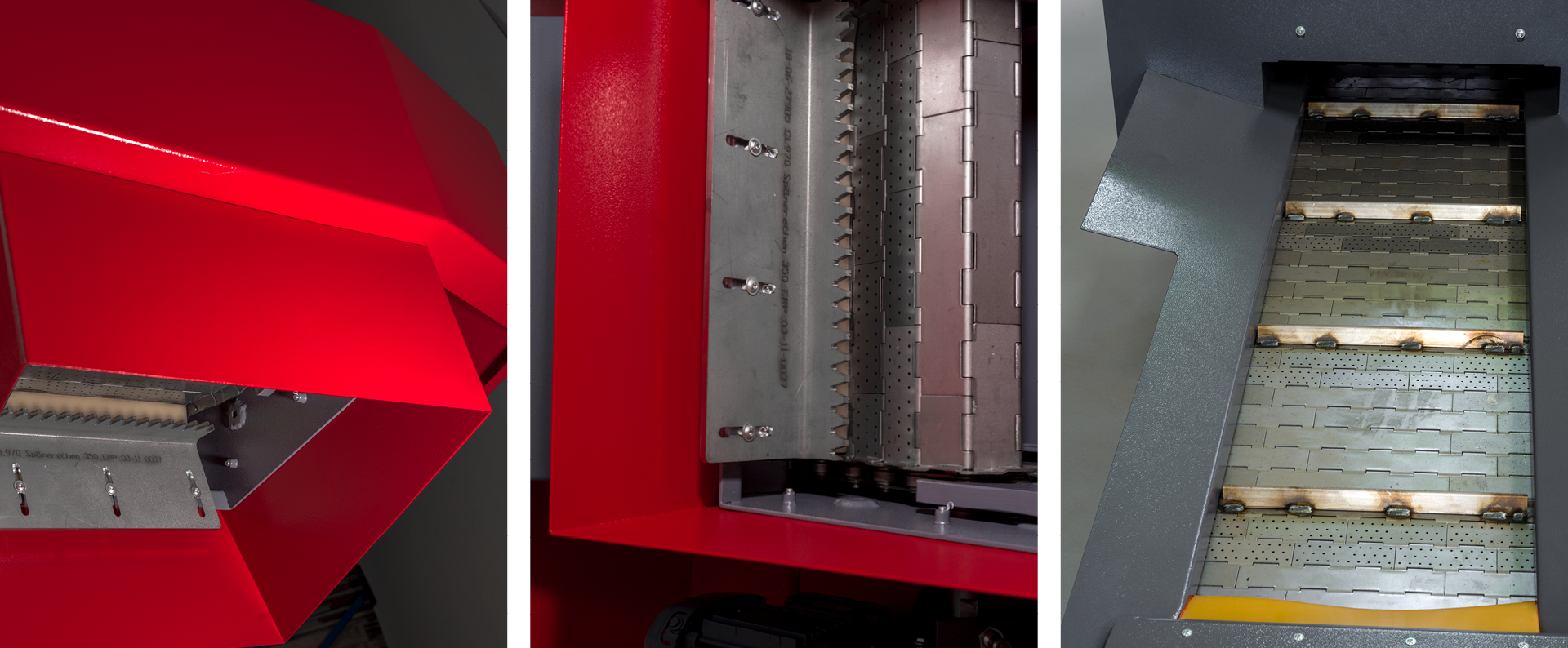


Chip conveyor categories
As an assembly of a machine tool, chipstream chip conveyors transport chips from the work area into a collection container. Ideally, depending on the design and size of the chip conveyor, chips and cooling lubricant are separated. The chipstream chip conveyors are available in numerous designs: as slat-band conveyors or scraper belt conveyors, with or without integrated chip pre-separation, as a pure push-in conveyor or in conjunction with an additional tank that is connected to the machine tank.
As an extended expansion stage under our combistream product brand, we also combine the properties of the chipstream chip conveyors with our outstanding expertise in the design and development of high-pressure systems for machine tools. combistream stands for maximum space utilisation with maximum possible automation for your production.
All chipstream and combistream systems with their corresponding chip conveyor concepts can be used on a wide range of machine tools for metal and plastic machining, e.g. sliding headstock automatic lathes, short turning machines, single-spindle lathes, machining centres and multi-spindle machines. Advantages: Increased productivity, avoidance of accident risks, recovery of cooling lubricant and raw materials (cost reduction), and much more.
Advantages of Müller chipstream and combistream chip conveyors
Additional advantages of combistream Chip conveyors with high pressure
Function and problem solving
Müller Chip conveyor technology / belts | Material / Chip types | Characteristics | Solution |
---|---|---|---|
Hinged belt conveyor | This conveyor is suitable for mixed chips from long to short and for all conventional chip types. If the mixing ratio of short and fine chips is very high compared to the number of long chips, a combination conveyor is recommended; the same applies to floating, short chips. | Chip conveyor concept BK10
| chipstream CST1 with BK10 Suitable for:
|
Scraper belt conveyor | This conveyor is only suitable for very short chips with a maximum length of 3-5 mm. It can handle all types of material well. | Chip conveyor concept BK11
| chipstream CST1 with BK11 Suitable for:
|
Combination conveyor consisting of hinged belt, pre-separation and scraper discharge | This combination conveyor is a true master in its class. Whether long-chipping or short-chipping, whether steel or brass - it ensures effective dirt removal and reliably protects the machine tank from contamination. | Chip conveyor concept BK20
| chipstream CST2 with BK20 Suitable for:
|
Combination conveyor consisting of scraper belt with top-mounted slotted screen, pre-separation and scraper discharge (cascade) | The cascading alternative is ideal for applications with short-chipping materials and in particular for the timely collection and removal of floating chips. The pre-filtration cascade consists of an upper and a lower slotted screen, which offers a great deal of flexibility to achieve optimum chip removal results. Suitable for all materials with a maximum chip length of 3-5 mm. | Chip conveyor concept BK21
| chipstream CST2 with BK21 Suitable for:
|
Chip conveyor technology
It is not uncommon for different materials to be processed and different types of chips to be produced on the same machine. The ideal solution would be to use the right chip conveyor for each type of chip. With combistream, we offer you modern chip conveyor technologies for a wide variety of chip types. Practical experience shows that the following three basic concepts are ideally suited to a wide range of application situations and can be implemented for various machine types. This does not mean that other chip conveyor technologies cannot be used in exceptional cases:
Basic concept 1
Work area conveyor as scraper or slat-band conveyor with large lubricoolant outlet and integrated chip collection basket below the outlet is very suitable for high chip volumes:
- high chip volumes.
- as few different materials and chip types as possible in order to determine chip conveyors in the best possible way.
- normal and medium degree of machine contamination due to rather large and coarse chips or readiness for increased dirt tank cleaning with very fine materials.
- Medium maintenance effort for the entire system (cleaning of the machine tank depending on the degree of soiling, but no more than once a month).
Recommended for | material | Chip conveyor |
---|---|---|
Normal and medium degree of machine contamination | Steels and hard alloys, different chips from long to short | Hinged belt conveyor (BK10) |
High degree of machine contamination | Brass, aluminium and other very fine-chipping materials | Scraper belt conveyor (BK11) |
Basic concept 2
Work area conveyor as scraper or slat-band conveyor with large lubricoolant outlet directly into an integrated pre-separation via slotted screens with automated chip discharge via a scraper conveyor is very well suited for high chip volumes:
- high chip volumes.
- as many different materials and chip types as possible, so that the pre-separation principle can be used effectively.
- a medium degree of machine soiling, especially due to fine and floating chips. The aim is to avoid frequent cleaning of the dirt tank.
- Medium maintenance effort for the entire system (cleaning of the machine tank depending on the degree of soiling, but no more than four times a year).
Recommended for | material | Chip conveyor |
---|---|---|
Medium degree of machine contamination | Steels and hard alloys, different chips from long to short | Hinged belt conveyor (BK20) |
Only fine and floating chips | Brass, aluminium and other very fine-chipping materials | Machine room: Scraper belt conveyor Dirt tank: Scraper belt conveyor (BK21) |
Basic concept 3
Work area conveyors as scraper or slat-band conveyors with a large lubricoolant outlet directly into the machine tank in combination with bottom cleaning of the machine tank by a scraper conveyor (usually in conjunction with full-flow filtration systems) are very suitable for high chip volumes:
- high chip volumes.
- frequently changing materials, various chip types that can be discharged in the best possible way using basic concept 3.
- a high degree of machine contamination due to fine chips and sludge.
- specific to brass and aluminium, possibly plastics.
- Low maintenance requirements (cleaning of the machine tank depending on the degree of soiling, but no more than twice a year).
Recommended for | material | Chip conveyor |
---|---|---|
All materials, all chip types, for frequently changing machining operations | Steels and hard alloys. Very different chips from long to short. Frequent material changes | Machine room: Hinged belt conveyor Dirt tank: Scraper belt conveyor (BK30) |
Only fine and floating chips | Brass, aluminium and other very fine chip materials | Machine room: Scraper belt conveyor Dirt tank: Scraper belt conveyor (BK31) |
CHIP CONVEYOR VERSUS COMBINED SYSTEM
Infeed conveyors are an excellent choice for successfully transporting chips from the machine's work area to the chip bucket. The question that concerns many users when purchasing a machine tool is whether there are more effective concepts than a simple slide-in conveyor with its sometimes limited options. At Müller, we therefore also offer our Chip conveyors in combination with an additional tank or directly integrated into the machine tank.
What are the main advantages of this?
- Larger quantity of coolant in circulation
- Chip residues remain in the additional tank and enter the machine tank more slowly or not at all
- When the machine tank is replaced, the floor can be cleaned, which greatly reduces maintenance intensity
- Better space conditions with maximum compactness enable better control over chip removal, especially with floating chips
- Optimum utilisation of the space around the machine thanks to the best possible combination of high-pressure system and cooling with the chip conveyor unit
The following matrix will help you to select the right product for your requirements.
CST1 | CST2 | CS2 | CS3 | CS4 | |
---|---|---|---|---|---|
Hinged belt conveyor (BK10) - Long-chip | • | • | • | • | • |
Scraper belt conveyor (BK11) - Short-chip | • | • | • | • | • |
Combination conveyor (BK20/21) | • | • | • | • | |
Combination conveyor with floor cleaning (BK30/31) | • | • | |||
Additional tank or machine tank integrated | • | • | • | • | |
Floating chips | • | • | • | • | |
Frequency-directed belt control | • | • | • | • | • |
Long part version (supportable) | • | • | • | • | • |
Integrable low pressure supply | • | • | • | • | |
Self-cleaning suction protection low pressure | • | ||||
Integrated high-pressure supply | • | • | • | ||
Integrated bypass filtration | • | • | |||
Integrated full-flow filtration | • | ||||
eco+ maximum energy efficiency | • | • | • | ||
Integrated plate heat exchanger | • | • | |||
Integrated active cooler | • |
Core competences + unique selling points
What is a Chip conveyor?
A Chip conveyor is a device used in industrial applications to transport and dispose of metal chips or other material waste produced during the processing of metals or other materials. As an assembly of a machine tool, a Chip conveyor transports chips from the work area into a collection container. Ideally, the chips are separated from the cooling lubricant.
Chip conveyors come in different shapes and sizes, depending on the requirements of the specific application. Typically, a chip conveyor consists of a conveyor belt, screw conveyor or similar mechanical system that transports the chips from the machining point to a central collection point or disposal area. This not only helps to keep the workplace clean, but also ensures safety, as loose chips can often pose a potential hazard to employees.
Chip conveyors are widely used in various industries, including metalworking, automotive, aerospace and other metalworking sectors.