Cooling lubricant filtration technologies
Cooling lubricant filtration technologies
Why coolant lubricant (CL) filtration?
Machining produces residues such as chips, sludge, abrasion, dust and much more, which contaminate the cooling lubricant. Effective coolant lubricant filtration prevents damage to pumps, valves, hoses, workpieces, tools, spindles, etc.. This prevents machine tool downtime, high maintenance and service costs, component wear and much more. Waste is also reduced and the service life of the cooling lubricant is increased many times over. Cooling lubricant filtration increases profitability in machining and sustainable management.
Filtration: our core expertise - your success factor, thanks in part to
Clean cooling lubricant at the cutting edge of the tool
Improved surface quality during machining
Avoidance of damage to the pump and therefore expensive downtimes and service costs
Which filter for which application?
This is one of the most frequently asked questions when configuring a cooling lubricant or high-pressure cooling lubricant system for machine tools. The task of a filter has been clearly described above. In order to fulfil these requirements, many roads lead to Rome, as one might say colloquially. Sometimes, however, it is also a question of how you want to deal with the issue yourself. The four models we have listed below as the preferred filter types all fulfil their purpose perfectly. It's the way they do it that makes the difference.
When it comes to exchangeable or spin-on and cascade filters, we have developed our own filtration system. While hydrostatic filters such as fleece and bag filters clean by gravity, hydrodynamic filters push the medium through. They also utilise filter cake for further improved filtration. They save space, increase machine running times and are also washable in the wire mesh version. In an ultrasonic bath with backwashing with air or clean medium, they are even as good as new.
Hydrodynamic filters:
- Müller exchangeable filter system
- Müller cascade filter system
- Müller automatic filter system
Hydrostatic filters:
- Müller compact belt filter
- Müller hydrocyclone filter
The Müller filter elements with their enlarged filter surface significantly improve efficiency - service life is increased many times over.
Significantly reduce machine downtimes and filter changes. When using a double changeover filter, the filter can be changed during operation.
Our washable wire mesh elements are easy to clean in an ultrasonic bath, which leads to sustainable use without disposal and reduces operating costs.
Flushing capacities up to 30 l/min. | Rinsing capacities up to 60 l/min. | Rinsing capacities up to 400 l/min. | Free of consumables | |
---|---|---|---|---|
Exchangeable filter (also as double changeover filter) | 10 µm - 60 µm | Yes | ||
Cascade filter | 10 µm - 60 µm | 10 µm - 60 µm | Yes | |
Automatic filter | 10 µm - 30 µm | 10 µm - 40 µm | 30 µm - 40 µm | Yes |
Compact band filter | Not useful for economic reasons | 30 µm - 60 µm | no |
Why do we not offer bag filters and only offer the compact belt filter for higher flushing capacities?
Bag filters are primarily made of polymer materials. They are certainly effective as a filter medium, but are difficult to change. When changing them, the periphery tends to become contaminated and, unfortunately, contaminated medium often gets into the clean area when the filter is changed. This is also the reason why we have developed our own technology that allows the user to pull the filter element upwards out of a closed area. This prevents dirt from reaching the clean side. The strength of the element means it is easy to change and does not tend to kink or overflow during replacement.
The compact belt filter is one of the most established and, if designed and manufactured to a high quality with overflow protection, one of the most reliable filters in the field of cooling lubricant filtration. It requires a filter fleece as a carrier material, which offers a high degree of autonomy, but still needs to be replaced from time to time. In our opinion, this filter is not justified for low flow rates. Here, the exchangeable and cascade filters we have developed appear to be more economical for the user than the relatively expensive compact belt filter with consumables. At high rinsing capacities of well over 60 l/min, the compact belt filter begins to show its advantages over other filter solutions, above all in the significantly more favourable production cost range in comparison with automatic filters, for example. In the end, the question arises as to what result you want to achieve: filtration without consumables and an uninterrupted machining process or a cheaper variant with filter fleece as the consumable medium.
We offer you the following filtration technologies as core competences for the filtration of cooling lubricant on our high-pressure systems and fluid systems:
Backwashable automatic filter
Our self-cleaning automatic filter. The ultimate in economy and ecology!

100% GREEN FILTRATION
We have been working with our self-cleaning automatic filters since the 2000s. Thousands of customers worldwide benefit from maximum purity of up to 20 μm. The filter is automatically cleaned by backwashing with air and its own medium. Experience shows that the medium purity in the clean tank is usually exceeded by up to 15 μm thanks to the filter cake. The automatic filter enables low-maintenance, reliable and sustainable operation. We currently offer three filter sizes as standard, which reliably clean up to 30 l/min at 30 μm, 60 l/min at 40 μm and 130 l/min at 40 μm. Customised solutions can be offered.
The low-maintenance, backwashable automatic filter is suitable for full and off-line filtration of all materials and cooling lubricants. The medium flows through the filter from the outside to the inside, dirt adheres to the sintered stainless steel mesh on the outside and falls to the bottom. The filter is cleaned automatically by backwashing with air or its own medium.
Thanks to different sizes and combinability, both small and very high flow rates can be filtered effectively, without medium and reliably.
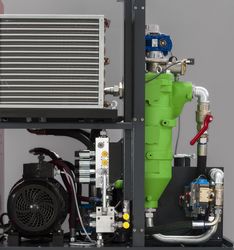

- Contaminated medium flows through the filter element at A from the outside to the inside. Dirt particles stick to the wire mesh element and are separated.
- The cleaned medium flows via outlet B into the clean tank or directly to the consumer.
- If the filter is saturated, an automatic cleaning cycle is triggered. The ball valve in C opens and allows the dirt to drain downwards towards the sludge box or chip conveyor. At the same time, motor D rotates the sintered filter element and it is blown out via the air bar E. The air, dirt and residual media mixture is discharged via C.
- Filtration performance is actually higher than nominally specified by the filter fineness. This is made possible by the filter cake that builds up in the element and the hydrostatic effect of pressurised filters (e.g. 30 µm nominal can mean up to 15 µm real)
Filter can also be installed horizontally
Filter works practically maintenance and consumable-free
Automatic filter model overview
AF - C1 | AF - C2 | AF - C3 | |
---|---|---|---|
Appearance | ![]() | ![]() | ![]() |
USP |
|
|
|
Performance data |
|
|
|
Automatic filter application:
- Cutting oils, water emulsions, synthetic cooling lubricants, biological cooling lubricants
- Medium to high degree of contamination of the cooling lubricant (e.g. high proportion of suspended particles)
- Flushing capacities up to 400 l/min. (several filters combined)
- In particular: Aluminium, brass and hard alloys, as well as machinable plastics
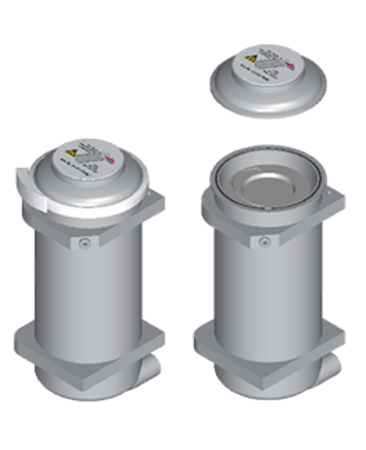
In terms of acquisition costs, the spin-on filter as a cartridge or bag filter is the cheapest option. The filtration performance generally depends on the medium. The maintenance costs can be quite high depending on the amount of use and soiling.
For this very reason, spin-on filters are avoided for high flushing capacities and for full or bypass filtration and are generally used as pre- or post-filters to protect the pump or other devices. The spin-on filter is very flexible in terms of filter fineness with purities of up to 10 μm.
Our replaceable filter element - three times the surface area for maximum filtration
Based on our own innovative strength and expertise, we have developed our own replaceable filter elements. The conventional commercial solutions did not fulfil our expectations in terms of service life and medium purity. The Müller exchangeable filter element is unique in the class of compact high-pressure devices. The three times larger filter surface guarantees even greater efficiency - because more filter surface means longer service life.
In addition, the wire mesh element is washable and can even be cleaned in an ultrasonic bath. Disposal, as is necessary with bag filters, for example, is not necessary. This is sustainable and reduces operating costs at the same time. These filters are standard in the compact high-pressure cooling lubricant filtration solutions.
Proprietary exchangeable filter system up to 60 l/min with high filter surface thanks to innovative pleating technology
- Used in Müller's dynamic pressure filter (medium is forced through the filter element under pressure)
- Long service life compared to other, comparable filters
- Quick, easy and clean to change
- Closed filter system (no risk of introducing dirt into the clean area when changing the filter)
- All wire mesh elements can be washed out and reused several times
- Large filter surface area compared to other cartridge solutions
- Very good price-performance ratio
- No hazardous waste - 100% recyclable
How exchangeable filters work
The way it works is as follows: a transfer pump draws in the contaminated medium in the machine tool tank and presses it through the closed, hydrostatic filter housing. The dirt particles adhere to the outside of the element. The cleaned cooling lubricant reaches the clean tank area via a riser pipe. The pumps then draw in from the clean area. When the control system receives a message via the differential pressure switch that the filter element has almost reached its intake level, a filter change alarm is triggered on the machine tool.
To avoid machine downtime due to the filter change process, it is advisable to install a double changeover filter, which is available from us for almost all machine models. This allows the filter change or filter maintenance to be carried out during operation.
As part of our Industry 4.0 partnership with the machine tool industry, we offer a pre-alarm on almost all models, which indicates the 80% saturation level of the filter and thus makes it possible to plan the maintenance cycle during shift operation.
Characteristic | Glass fibre (25 μm) | Wire mesh (25 μm) | Wire mesh (40 + 60 μm) |
---|---|---|---|
Reusability | Limited | Multiple | Multiple |
Degree of separation | High | Medium | Medium |
Recycling | Contains polymer materials | 100% metal | 100% metal |
Filter area | 18,000 - 22,000 cm² | 18,000 cm² | 18,000 cm² |
Application | Cooling lubricants | Cooling lubricants | Cooling lubricants |
Special features | Must be replaced after use | Good cleaning in ultrasonic bath | Hand washable, good cleaning in ultrasonic bath |
In a cascade filter, the medium is cleaned via a filter cascade consisting of a pre-filter and fine filter. The medium first flows through the coarse pre-filter, which is occasionally washed out (mesh density approx. 500 μm). This builds up a filter cake (increasing separation efficiency and filter fineness). In the second step, the pre-cleaned medium passes through the fine filter. Purities of up to 20 μm can be achieved. Either washable wire mesh elements or spin-on filters (glass fibre) are used as fine filters. This filter is particularly suitable for higher flushing capacities of up to 60 l/min and is therefore an excellent alternative to bag filters or small compact belt filters.
How the cascade filter works
- Cartridge A, the pre-filter, consisting of a 500 µm steel mesh, is flushed with cooling lubricant from the outside to the inside under number 1
- Cartridge B, the downstream fine filter with different filter finenesses (60 - 25 µm), is then flushed from the outside to the inside with pre-cleaned medium from cartridge A
- In cartridge A, the degree of contamination of the filter is measured at point number 2 using a differential pressure switch. An alarm is triggered if the level of contamination is too high
- In cartridge B, the degree of contamination is monitored at point number 3 with a pressure switch. An alarm is triggered if the level of contamination is too high
- The filter elements can be easily replaced or removed for cleaning at A and B (see picture)
- This type of filtration is suitable for medium to high flushing capacities, but is not recommended for full-flow filtration
- Depending on the type of fine filter cartridge, medium-free filtration is possible

How the compact belt filter works
Hydrostatic pressure builds up on the filter medium and the filtrate flows downwards through the filter medium. The solids are deposited on the filter medium. The drive by means of a geared motor and thus the consumption of the filter medium is controlled by a float switch, depending on the level of soiling.